Автор статьи
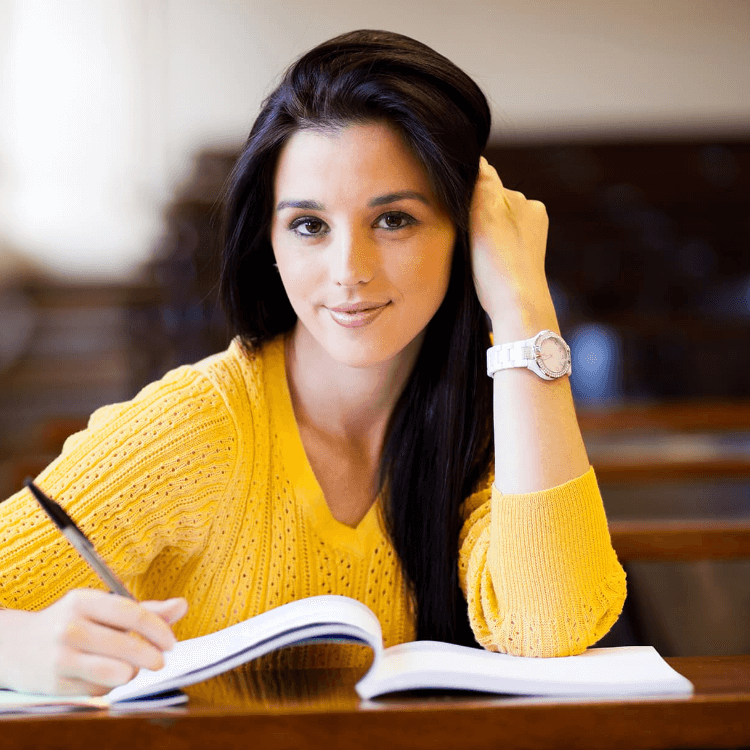
Валерия
Эксперт по сдаче вступительных испытаний в ВУЗах
2. Особенности технической обработки деталей ТВЧ.
Представим себе проводник электрического тока, на¬пример в виде медной трубки, свернутой в незамкнутое кольцо. Внутрь такого кольца вставили металлический стержень так, чтобы он не касался трубки. Если теперь концы трубки включить в цепь переменного тока высо¬кой частоты, то появится переменное электромагнитное поле такой же частоты. Силовые линии поля будут пронизывать стержень, благодаря чему в нем возникнет пе-ременный ток высокой частоты. Это так назы¬ваемые вихревые токи Фуко. Такой способ наведения пе¬ременного тока в проводнике без непосредственного включения его в электрическую цепь называется элект¬ромагнитной индукцией, а медная трубка, которая ис-пользуется для нагрева, — индуктором. Индукция в пе¬реводе с английского значит наведение. Особенностью тока высокой частоты является то, что он проходит не по всему сечению проводника, а только у его поверхности. При этом, чем выше частота тока, тем меньше глубина его проникновения в поверхность. Прохождение тока по проводнику, как известно, сопровождается выделением теплоты. Роль такого проводника выполняет нагреваемая деталь. Поскольку ток проходит только по ее поверхности, то и нагревается не вся де¬таль, а лишь ее поверхность. Продолжительность нагре¬ва поверхности до закалочной температуры очень не¬большая, обычно 1 -10 с. Во избежание нагрева индук¬тора внутри его циркулирует проточная вода. Если нагретую до закалочной температуры поверх¬ность детали быстро охладить, например, с помощью во¬дяного душа, то произойдет поверхностная закалка. Та¬ким образом, закалка ТВЧ, или, как ее иногда называют, индукционная закалка, это по существу поверхност¬ная закалка, отличающаяся лишь способом нагрева деталей. При закалке ТВЧ применяют три метода: одновре¬менный, последовательный, непрерывно-последователь¬ный. Одновременный метод заключается в том, что зака¬ливаемая деталь устанавливается в индуктор и нагрева¬ется одновременно по всей поверхности, которую нужно закаливать. Этот метод применяют для деталей с не¬большой поверхностью (втулок, пальцев, роликов и т. п.). Если деталь круглой формы, то для более равномерного нагрева ее приводят во вращение. После нагрева до тре¬буемой температуры индуктор отключается, и автома¬тически включается подача охлаждающей воды. Ох¬лаждение, как и нагрев, проводится одновременно по всей поверхности. При таком методе обработки целесо¬образно охлаждающую воду подавать через спрейерное устройство, смонтированное в самом индукторе. С этой целью внутренняя часть индуктора выполняется в виде двух кольцевых камер. В наружной камере циркулирует вода, охлаждающая индуктор в период нагрева детали, а во внутреннюю вода подается только в период охлажде¬ния детали, когда индуктор отключен. На внутренней стен-ке этой камеры, обращенной к поверхности детали, имеет¬ся множество отверстий, через которые вода тонкими струйками подается на поверхность детали. Последовательный метод обработки предусматривает последовательную (поочередную) закалку отдельных элементов детали, например шеек коленчатого вала или зубьев крупных шестерен (зуб за зубом). Применение такого метода позволяет упростить конструкцию индук¬тора и снизить потребную мощность высокочастотного генератора. Непрерывно-последовательный метод обработки сос¬тоит в том, что индуктор непрерывно перемещается от¬носительно детали, а за индуктором движется сблокиро¬ванное с ним охлаждающее устройство в виде спрейера. Таким образом последовательно нагрева¬ется и закаливается вся поверхность детали. Если де¬таль имеет круглую форму, то для большей равномерно¬сти нагрева она вращается вокруг своей оси. Такой метод обработки применяют для деталей, име¬ющих сравнительно большую закаливаемую поверх¬ность, например длинных валов, направляющих станин и др. В этих случаях для одновременного нагрева мощ¬ность генератора может оказаться недостаточной, либо индуктор получается неконструктивных размеров. Для закалки этим методом плоских поверхностей применяют петлевые индукторы.3. Особенности процессов шлифования наружных поверхностей детали.
Шлифование – процесс обработки заготовок резанием с помощью инструментов (кругов), состоящих из абразивного материала. Абразивные зерна расположены беспорядочно. При вращательном движении в зоне контакта с заготовкой часть зерен срезает материал в виде очень большого числа тонких стружек (до 100000000 в минуту). Процесс резания каждым зерном осуществляется мгновенно. Обработанная поверхность представляет собой совокупность микроследов абразивных зерен и имеет малую шероховатость. Шлифование применяют для чистовой и отделочной обработки деталей с высокой точностью. Главным движением при шлифовании является вращение шлифовального круга, а перемещение круга относительно детали является движением подачи. Различают следующие основные виды шлифования: плоское, круглое, внутреннее. Плоское шлифование При плоском шлифовании (рисунок, позиция а) возвратно-поступательное движение заготовок необходимо для обеспечения продольной подачиSпр. Для обработки поверхности на всю ширину b заготовка или круг должны иметь поперечную подачу Dsп , которая осуществляется прерывисто при крайних положениях заготовки в конце продольного хода. Периодически осуществляется движение вертикальной подачи Dsb , в крайних положениях заготовки в конце поперечного хода. Плоское шлифование может осуществляться периферией или торцом шлифовального круга. Круглое шлифование При круглом шлифовании (рисунок, позиция б) движение продольной подачи осуществляется возвратно-поступательным перемещением заготовки. Подача Sпр соответствует осевому перемещению заготовки за один ее оборот. Вращение заготовки является движением круговой подачи. Подача Sп на глубину резания происходит при крайних положениях заготовки. Движения, осуществляемые при внутреннем шлифовании показаны на рисунке, позиции в. Виды шлифования Для выполнения процесса шлифования наружных поверхностей деталей используются кругло-шлифовальные, плоско-шлифовальные и бесцентрово-шлифовальные станки. Для обработки сложных фасонных поверхностей используются специальные лентошлифовальные станки. В лентошлифовальных станках применяется инструмент в виде бесконечной абразивной ленты. Лента в процессе шлифования поверхности сложной формы (например, лопатки турбин) огибает сложную поверхность и перемещается в осевом и продольном направлениях. Абразивный слой наносят на бумажную или тканевую основу ленты. Шлифованием обрабатываются только жесткие детали, не формирующиеся в процессе обработки. Данный способ не допускает обработки малых отверстий.4. Пути уменьшения припусков.
Изготовление заготовок с заусенцами и следами облоя приводит к значительным погрешностям установки их на станке и, следовательно, увеличивает припуски на обработке. Значительные колебания припусков приводят к упругим отжатиям в технологической системе и копированию исходных погрешностей, что в свою очередь приводит к увеличению припусков на чистовые операции. В этих условиях приходится вводить дополнительные чер¬новые и чистовые операции. Изготовление заготовок с минимальными припусками возможно при развитии малоотходной технологии производства заготовок. Применение точных заготовок, форма которых приближена к форме готовых деталей, позволяет уменьшить погрешность установки деталей на станке и равномерно распределить припуск по всему периметру обрабатываемой поверхности. Малые и равномерные припуски позволяют упростить технологический процесс обработки и в некоторых случаях исключить черновые операции, при которых снимается наибольший припуск, а также ис¬пользовать сразу методы чистовой обработки с высокими режимами резания и минимальными припусками. Применение принципиально новых методов и технологических процессов изготовления заготовок позволяет значительно сократить расход конструкционных материалов. Внедрение технологии малоотходного производства заготовок, в свою очередь, способствует интенсификации механической обработки и внедрению прогрессивных методов обработки. Техническое перевооружение кузнечно-штамповочного производства, в частности применение поперечно-винтовой прокатки, многопозиционных горячевысадочных автоматов, штамповки в разъемных матрицах и др., позволяет уменьшить расход металла и получить заготовки с лучшим расположением волокон. Для обеспечения постоянства объема заготовки и повышения точности поковок в автоматы могут быть встроены мини-ЭВМ. Широкое развитие получает штам¬повка зубчатых колес с предварительным образованием зубьев и отверстий, то есть в этом случае оставляется минимальный припуск под обработку резанием. Таким образом, значительно сокращается не только расход мате¬риала, но и технологический процесс обработки зубчатого колеса, в частности, при обработке базового отверстия можно применить прогрессивный процесс протягивания, а при обработке зубьев – чистовое фрезерование. Применение операций порошковой металлургии позволяет значи¬тельно сократить припуски на механическую обработку. Высокая точность, полученная при изготовлении заготовок, позволяет значительно сократить их механическую обработку и лишь после химико-термической обработки применить доводочные операции. При объемной холодной штамповке коэффициент использования металла может быть доведен до единицы, например, при изготовлении мегизов из бунтового металла на холодновысадочных автоматах при дальнейшем накатывании резьбы. Таким образом, припуск на механическую обработку в этом случае равен нулю. Изготовление заготовок конических шестерен методом холодной объемной штамповки позволяет уменьшить припуск на обработку зубьев до 0,2 мм. К числу основных процессов малоотходной технологии производства заготовок относятся и комбинированные способы получении готовок. Например, для заготовок простой формы сварка трением сводит к минимуму термические деформации, отходы металла и припуски на механическую обработку. В частности, комбинированым способом изготовляют скользящую вилку кардана автомобиля. В некоторых случаях замена стальных поковок отливками из высокопрочного чугуна с шаровидным графиком позволяет сократить перевод металла в стружку на 60%. Значительное сокращение расхода металла в стружку возможно при замене процесса резания пластическим деформированием. Например, накатывание вместо нарезания резьбы и шлицев, прикатка зубьев колес взамен шевингования, выдавливание фасок по периметру шлицевого отверстия вместо резания и др. Новым направлением в технологии обработки как металлических так и неметаллических деталей можно считать внедрение лазеров. Луч лазера можно сфокусировать в точку, размер которой составляет сотые доли миллиметра, и достигнуть температуры в сотни тысяч градусов. В частности, возможность сваривать термообработанные изделия без их разупрочнения позволяет значительно изменить технологический процесс изготовления некоторых изделий. Деформации, вызываемые термической обработкой деталей, вынуждают оставлять значительные припуски на дальнейшую обработку деталей. Применение лазеров позволит устранить деформацию деталей и в ряде случаев необходимость механической обработки после термической обработки. Электрофизические и электрохимические методы позволяют обрабатывать заготовки сложной формы и из труднообрабатываемых материалов. Например, электрохимическое удаление заусенцев при производстве шестерен позволяет достигнуть высокого качества кромок без применения процессов резания. Комбинированные методы находят все более широкое распространение не только при изготовлении заготовок, но и при их механической обработке. В качестве примера рассмотрим процесс протягивания отверстий комбинированным инструментом. При изготовлении зубчатых колес обработка отверстий влияет на качество изделия в целом. Применение заготовок с прошитым отверстием позволяет включить несколько предварительных операций (сверление и зенкерование) и сразу осуществить протягивание отверстий. Требования малоотходной технологии отразились и на конструкции протяжного инструмента. В частности, деформирующее протягивание, кроме окончательной и промежуточной операции, может являться и подготовительной операцией, предшествующей дальнейшей обработке отверстий резанием, причем припуск на последующую обработку отверстия резанием может быть значительно уменьшен. Применение деформирующих протяжек позволяет уменьшить расход металла до 30% и сократить обработку резанием, необходимую удаления дефектного поверхностного слоя. Различные комбинации деформирующих и режущих элементов позволяют не только уменьшить припуски на дальнейшую обработку отверстий, но и в ряде случаев исключить ее полностью вследствие полного удаления заданного припуска на операции протягивания. Применять комбинированное протягивание можно для широкой номенклатуры деталей, например, для обработки отверстий в коромысле пиана двигателя внутреннего сгорания, поворотного кулака передней оси трактора, цилиндра амортизаторов мотоциклов, легковых и грузовых автомобилей, втулки звена гусеницы трактора, внутренних колец подшипников, деталей типа труб и цилиндров и т.д. Достижения в области малоотходной технологии позволяют получить более точные заготовки и интенсифицировать процесс механической обработки. Значительное сокращение припусков на обработку, а, следовательно, и сокращение расходов металла, может быть достигнуто при переходе на принципиально новые технологические процессы; при этом припуск на механическую обработку не должен превышать 1,5 мм на сторону.5. Поточная сборка.
Под поточной линией сборки понимается ряд рабочих мест, участвующих в сборке сборочных единиц, расположенных последовательно операциям технологического процесса сборки и впуск готовых изделий через определенный промежуток времени. Она может быть осуществлена как при подвижном так и неподвижном объекте сборки. Поточная сборка имеет два вида: поточная подвижная и поточная неподвижная. Темп – расчетный промежуток времени, через к-рый с поточной линии должна выпускаться единица продукции. Темп (t) зависит от выпуска и определяется фондом времени (T) (год, смена) за тотже период времени. Собираемый объект перемещают от одного раб.места к др.: 1) ручную (на тележках); 2) с помощью конвейеров. Рабочий идет вдоль конвейера или перемещается в месте с ним. Число рабочих на каждом рабочем месте зависит от трудоемкости операций. Производительность раб.места: Q=T1×B/tшт, где T1- время производительности(час), B-число рабочих на сборочном месте, tшт-время на перемещение изделия. Переход на поточный метод производства позволяет увеличить выпуск продукции, снизить себестоимость изделия, увеличить производительность труда. Непрерывность процесса при поточной сборке достигается благодаря равенству или кратности времени выполнения операций на всех рабочих местах, т.е. длительность любой сборочной операции на линии сборки должна быть равна или кратна такту сборки изделия. Поточная сборка явл-ся наиболее совершенной по технико-экономическим показателям при расчлененном процессе с принудительным движением объекта. Для достижения высокой производительности труда и высокого качества работ при поточной сборке, требуется большое кол-во инструментов и приспособлений.6. Определение числа производственных рабочих мест механосборочного цеха
Промышленно-производственный персонал цеха состоит из производственных и вспомогательных рабочих, инже¬нерно-технических работников, служащих и младшего обслужи¬вающего персонала. Состав и количество работающих опреде¬ляют по следующей схеме: определяют количество работающих, непосредственно связан¬ных с выпуском продукции в подразделении (основные рабочие); находят количество персонала, обеспечивающего работоспо¬собность оборудования (основного оборудования, транспортно-складской системы, средств вычислительной техники и др.); определяют число инженерно-технических работников; находят число работников вычислительного центра; определяют количество счетно-калькуляционного и младшего обслуживающего персонала. Для того чтобы определить состав и количество работающих, необходимо знать следующие показатели: программу цеха, вид изделий, типовые технологические процессы, серийность, наиме¬нование оборудования; его характеристики: надежность и слож¬ность наладки оборудования, сменность работы. Для механического цеха число основных производственных рабочих определяют следующим образом. Число станочников определяют либо по станкоемкости, либо по числу станков. По станкоемкости число станочников рассчитывают по фор¬муле По числу станков число станочников рассчитывают по формуле В формулах Рст — расчетное число производственных рабо¬чих данной профессии; Тст — годовая станкоемкость работ данного вида; Кр — коэффициент, определяющий трудоемкость ручных работ, Кр = 1,02 для массового, Кр = 1,05 для мелко¬серийного производства; Ф — эффективный годовой фонд вре¬мени рабочего; Км — коэффициент многостаночного обслужива¬ния, Км = 1 … 5 в зависимости от уровня автоматизации станков. Годовая станкоемкость работ где Фст — эффективный годовой фонд времени станка; S — количество станков; Кз. ср — средний коэффициент загрузки оборудования. Производственные рабочие автоматических линий — это опе¬раторы, выполняющие установку и снятие обрабатываемых де¬талей, наладчики, обеспечивающие нормальную работу автома¬тической линии. Их число не может быть определено расчетами по станкоемкости и по числу станков, для этого используют нормы технологического проектирования. На линиях с автомати¬ческой передачей деталей с линии на следующую операцию тре¬буется один оператор в смену, на линиях с ручной передачей деталей — два оператора в смену. Число наладчиков определяют исходя из норм обслуживания в зависимости от группы сложно¬сти наладки: для особо сложной на одного наладчика приходится два станка, для сложной — четыре, для средней — шесть, для простой — восемь. К общему числу производственных рабочих автоматических линий добавляют 50% запасных рабочих. При двухсменной работе число производственных рабочих делят по¬ровну между сменами. Определение числа вспомогательных рабочих механосборочного цеха. Число разметчиков и слесарей определяют по трудоемкости, принимаемой в процентах от трудоемкости станочных работ; для массового и крупносерийного производства — 1—3%, для среднесерийного и мелкосерийного — 5%, для единичного и мелкосерийного производства — до 10%. Численность вспомогательных рабочих может определяться по следующим параметрам: трудоемкости планируемого объема работ, числу рабочих мест, нормам обслуживания, в процентах от основных рабочих, в процентах от количества оборудования. При повышении уровня автоматизации растет доля вспомогатель¬ных рабочих. На стадии предварительного проектирования их число определяют по статистическим данным. В механических цехах средне- и мелкосерийного производства их 18—25% общего числа рабочих, в цехах массового производства 35—50%, на автоматических и поточных линиях — 50—55%. На стадии ра¬бочего проекта требуется точный расчет по всем категориям вспомогательных рабочих отдельно. Число наладчиков опре¬деляют по нормативам в зависимости от вида оборудования. Определение числа ИТР, служащих и младшего обслуживающего персонала механосборочного цеха. Численность инженерно-технических работников (администра¬ция цеха, сменные мастера, технологи, нормировщики, механики, специалисты в области вычислительной техники и средств автома¬тизации оборудования цеха) определяют по нормативам и расчет¬ным путем. Нормативы для определения численности ИТР в зави-симости от числа рабочих приведены в табл. 10.6. При резком сокращении числа основных рабочих в автомати¬зированных цехах также резко возрастает и число ИТР, связан¬ных со средствами автоматизации. Численность ИТР, занятых эксплуатацией средств вычислительной техники, определяют исходя из объема выполняемых работ, оснащенности средствами вычислительной и организационной техники. Если персонал вычислительного центра осуществляет только эксплуатацию ранее разработанного программно-информацион¬ного обеспечения АСУ и САПР, его численность определяют по формуле Нсу = 0,22Рп.п, где Рп.п — количество производствен¬ного персонала цеха. Когда персонал ВЦ участвует в разработке отдельных ком¬понент АСУ предприятия, число работников этой категории определяют исходя из объема выполняемых ими работ: где Пi — численность работников подразделе¬ния постановки и внедрения по j-му классу задач; Lij — число задач j-го класса, находящихся в разработке в течение года в i-м подразделении; Hij — средний норматив числа задач j-го класса, приходящихся на одного работника в i-м подразделении; Кср — коэффициент, учитывающий средний стаж персонала; m — количество задач j-го класса. Изменение структуры и функциональных возможностей вычис¬лительных средств различных типов (увеличение мощности персо¬нальных ЭВМ, упрощение эксплуатации вычислительной тех¬ники) приводит к тому, что в качестве оператора ЭВМ выступают технолог, конструктор, плановик, нормировщик. Поэтому ряд групп штатных единиц — операторы ЭВМ, работники подразде¬лений по обработке информации, работники отделов по подготовке данных — в небольших цеховых вычислительных центрах могут отсутствовать. Численность счетно-конторского персонала, куда входят бух¬галтеры, табельщики, учетчики, а также младший обслужива¬ющий персонал (уборщики, гардеробщики, курьеры), подсчиты¬вают по нормативам. Численность всех категорий работающих на стадии предвари¬тельного проектирования можно выбирать в процентах от общего числа рабочих: вспомогательных рабочих — 26—30%, инже¬нерно-технических работников — 10—12%, служащих — 2—3%, младшего обслуживающего персонала — 2—3%, контролеров (ИТР, рабочие) — 4—6% общего числа станков7. Принципы дифференциации и концентрации операций.
Метод расчленения операций техпроцесса на несколько более простых принято называть дифференциацией операций. Соединение же несколько простых операций в одну более сложную называется методом концентрации (укрепления) операций. При концентрации операций упрощается производственные планирование, так как учетными единицами при этом являются операции, число которых сокращается. Кроме того, уменьшается потребность в производственных площадях, количество оснастки, режущих инструментов, сокращается длительность технологического цикла, увеличивается производительность труда. Метод дифференциации ведет к упрощению оборудованию, оснастки, настройки станка. Предпочтительно его применение в условиях пуска производства в короткие сроки при слабой инструментальной базе предприятия, не дающей возможности своевременно произвести тщательную технологическую подготовку производства, что необходимо для реализации методом концентрации. В последнее время все больше развития находит метод концентрации операций посредством применения сложных высокопроизводительных многоинструментальных станков, станков с ЧПУ, обрабатывающих центров, гибких производственных систем и т.п.8. Методы обработки без снятия материала.
Методы обработки без снятия стружки все больше применяются при изготовлении деталей машин в связи с их высокой производительностью, способностью создавать поверхность с малой шероховатостью и необходимыми физико-механическими свойствами поверхностного слоя. Формы заготовок в современном производстве должны приближаться к формам готовых деталей. Методами обработки без снятия стружки получают только те поверхности, которые будут сопрягаться с поверхностями других деталей. Представляется возможность отказаться от традиционных методов обработки резанием. Производство деталей упрощается, отходы практически отсутствуют. Методы обработки без снятия стружки основаны на использовании пластических свойств металлов, т.е. способности металлических заготовок принимать остаточные деформации без нарушения целостности металла. Поверхность заготовки принимает требуемые форму и размеры в результате перераспределения элементарных объемов под воздействием инструмента. Исходный объем заготовки остается постоянным. В ходе обработки глобоидная форма кристаллов поверхности металлов может измениться, кристаллы сплющиваются в направлении деформирования, образуется упорядоченная структура волокнистого характера. Обработку методами без снятия стружки производят на многих металлообрабатывающих станках с помощью специальных инструментов. Ряд методов пластического деформирования легко поддается автоматизации. Сокращение или даже полное устранение некоторых отделочных операций при обработке пластическим деформированием снижает стоимость изготовления деталей. Основным ограничением для материалов при поверхностной пластической обработке (ППО) является величина относительного удлинения при растяжении, а также твердость материала обрабатываемой детали. Все применяемые в настоящее время ППО можно разделить на две основные группы: · статистические, способы, при которых силы прижимы постоянны; · динамические способы, при которых силы прижима периодически меняется во время обработки.9. Контроль качества собранных изделий
Сборка является заключительным этапом технологического процесса, от которого прямо или косвенно зависит качество изготовленных машин. Качество — понятие комплексное, распространяемое не только на изделие в целом, но и на его агрегаты, узлы и детали. Говоря о качестве, мы подразумеваем под этим, прежде всего, соответствие машины своему служебному назначению. Служебное же назначение машины, как известно, характеризуется определенной (для данного изделия) совокупностью технических, технологических и экономических показателей, к которым могут быть отнесены: производительность, металлоемкость, область применения , трудоемкость изготовления, долговечность и надежность, технологичность, себестоимость, уровень стандартизации и технической эстетики и т.п. Многие из указанных выше показателей, определяющих качество изделий, и в частности эксплуатационные свойства машин, зависят r основном от изготовления деталей машин, в процессе которого, даже при наличии технического контроля, допускаются некоторые погрешности (точности, формы и т.п.). Хотя в процессе сборки не ставится прямой задачи выявить погрешности, допущенные в процессе изготовления деталей, а лишь предусматривается в процессе технического контроля сборки не допустить погрешностей сопряжения деталей, все же приходится выполнять и косвенные задачи — выявлять погрешности, допущенные при механической обработке деталей, которые в той или иной мере могут повлиять на качество выполняемых сопряжений. Так же, как и погрешности изготовления деталей, погрешности сборки могут носить систематический и случайный характер и в зависимости от характера допускаемых отклонений могут быть подразделены на: — погрешности, вызываемые характером посадок (зазор, натяг и их отклонения); — погрешности, получаемые вследствие отклонений от установленных норм на взаимное положение отдельных элементов машины в процессе сборки (перекосы, биение, несоосность и т.п.); — погрешности, вызванные деформацией сопрягаемых деталей и их поверхностей (искажение формы детали, нарушение контакта сопрягаемых поверхностей, царапины и задиры на поверхностях деталей и т.п.); — погрешности, являющиеся результатом недостаточной жесткости деталей (ослабление креплений, нарушение связей, герметичности и т.д.); — погрешности, являющиеся следствием зарязненности рабочего места (опилки, абразив, замасливание и т.д.). Поэтому в процесс cборки и проверяются главным образом параметры, вызывающие указанные выше погрешности, и в частности: а) правильность взаимного положения отдельных элементов машины, приданного им в процессе сборки соответственно заданным техническим условиям (относительное положение, зазоры, соосность и т.п.); б) правильность затяжки резьбовых соединений, особенно на ответственных соединениях, где необходимо обеспечить герметичность; в) правильность комплектации деталей (наличие всех болтов, шплинтов и других деталей в собранном элементе машины); г) наличие недопустимых шумов, свидетельствующих о неправильном соединении деталей, или вызванных другими причинами; д) соответствующий техническим условиям внешний вид изделия или его отдельных элементов; с) наличие приемочных клейм контролеров на операциях, предшествующих данной, и т.п. Контроль в сборочных цехах осуществляют в процессе сборки узлов и изделий, притом основной контроль ведут сами сборщики (самоконтроль), поэтому большинство операций, которые проверяются самим исполнителем, не нуждаются в дополнительной проверке. В этом случае вся ответственность за качество сборки ложится на самого сборщика. Однако весьма часто выполнение контрольной операции невозможно осуществить в процессе сборки вследствие необходимости применения специальных контрольных приспособлений, продолжительности времени па выполнение контрольной операции, которое невозможно совместить с регламентированным темпом технологического процесса сборки. В этом случае контрольная операция выделяется в самостоятельную, для которой предусматривается в общем потоке рабочее место, при этом темп работы контролеров подчиняется темпу работы конвейера (потока). В том случае если темп работы контролера меньше темпа работы конвейера, рекомендуется совмещение нескольких контрольных операций но осуществлению так называемого «лучевого» (эпизодического) контроля. Для контроля обычно применяют различного вида мерительный инструмент и контрольные приспособления, которые обеспечивают объективность контроля. Тем не менее пока еще используются и субъективные методы контроля из-за недостаточного уровня производства измерительных средств. Внешний вид контроля при сборке — это проверка правильности взаимного положения деталей, в частности проверка правильности зазоров между сопрягаемыми элементами объекта сборки. Проверка этих зазоров может осуществляться следующими способами: щупами (с точностью до 0,4мм) и индикаторами, с помощью которых обнаруживается перемещение деталей в направлении зазора (с точностью до 0,01 мм). Это перемещение обычно называют «лифтом» или «качкой». Для проверки правильности зазоров и обеспечения удовлетворительной смазки трущихся поверхностей применяется измерение давление масла. вводимого в сопряжение — метод «опрессовки маслом» Кроме основных видов контроля. Могут применяться и дополнительные, суперконтроль для проверки (выборочный) уже принятых изделии и инспекционный контроль , осуществляемые лабораториями исследования качества, статистический контроль. Метод статистического контроля позволяет осуществить анализ и профилактику брака на операциях сборки на основании закономерностей математической статистики, систематизировать повторяемые случайные погрешности, допускаемые при сборке, на основе которых строится технологический процесс сборки, практически исключающий брак. Контрольные операции также должны снабжаться детальными инструкционными картами контроля, при помощи которых устанавливаются определенные, притом единые, требования для собираемого объекта. Заключительной контрольной операцией технологического процесса изготовления машины является ее испытание в искусственных, но близких к реальным условиям эксплуатации. Испытания узлов совмещают с процессом обкатки, в процессе которой обеспечивается приработка сопряженных деталей в подвижных соединениях (подшипники, зубчатые колеса и т.п.). Для испытания изделий и их узлов в настоящее время широко применяют специальные стенды.10. Типы и методы производства
Организация производственных процессов, выбор наибо¬лее рациональных методов подготовки, планирования и конт¬роля за производством во многом определяются типом произ¬водства на машиностроительном предприятии. Под типом производства понимается совокупность призна¬ков, определяющих организационно-техническую характери¬стику производственного процесса, осуществляемого на од¬ном или многих рабочих местах в масштабе участка, цеха, предприятия. Тип производства во многом предопределяет формы специализации и методы организации производствен¬ных процессов. В основу классификации типов производства положены следующие факторы: широта номенклатуры, объем выпуска, степень постоянства номенклатуры, характер загрузки рабо¬чих мест и их специализация. Номенклатура продукции представляет собой число Наиме¬нований изделий, закрепленных за производственной систе¬мой, и характеризует ее специализацию. Чем шире номенкла¬тура, тем менее специализирована система, и, наоборот, чем она уже, тем выше степень специализации. Широкая номенк¬латура выпускаемой продукции обусловливает большое раз¬нообразие технологических процессов и операций, оборудо¬вания , инструментов, оснастки и Профессий рабочих. Объем выпуска изделий — это количество изделий опре¬деленного вида, изготавливаемых производственной системой в течение определенного периода времени. Объем выпуска и трудоемкость изделия каждого вида оказывают решающее влияние на характер специализации этой сис¬темы. , Степень постоянства номенклатуры — это повторяемость изготовления изделия данного вида в последовательные пе¬риоды времени. Если в один плановый период времени изде¬лие данного вида выпускается, а в другие — не выпускается, то степень постоянства отсутствует. В зависимости от указанных выше факторов различают три типа производственных процессов или три типа производства: единичное, серийное и массовое. Каждому типу производства соответствуют: величина ука-занныхкоэффициентов, вид используемого оборудования, тех¬нология и формы организации производства, виды движений предметов труда, производственная структура предприятия (цеха, участка) и другие особенности. Единичное производство характеризуется широкой номен¬клатурой изделий и выпуском малых объемов одинаковых изде¬лий, повторное изготовление которых, как правило, не предус¬матривается. Это делает невозможным постоянное закрепле ние операций за отдельными рабочими местами, коэффициент специализации /Ссп > 40 деталеопераций на одно рабочее мес¬то. Специализация таких рабочих мест обусловлена только их технологической характеристикой и размерами обрабатывае¬мых изделий. При этом производстве применяют универсаль¬ное оборудование и в основном последовательный вид движе-ния партий деталей по операциям технологического процесса. Заводы имеют сложную производственную структуру, а цехи специализированы по Технологическому принципу. Серийное производство специализируется на изготовле¬нии ограниченной номенклатуры изделий сравнительно не¬большими объемами и повторяющимися через определенное время партиями (сериями). В зависимости от числа закрепля¬емых за каждым рабочим местом операций, регулярности по¬вторения партий изделий и их размера различают три подтипа (вида) серийного производства: мелкосерийное, среднесерий¬ное и крупносерийное. Мелкосерийное производство тяготеет к единичному: из¬делия выпускаются малыми сериями широкой номенклатуры, повторяемость изделий в программе завода либо отсутствует, либо нерегулярна, а размеры серий неустойчивы; предприя¬тие все время осваивает новые изделия и прекращает выпуск ранее освоенных. За рабочими местами закреплена широ¬кая номенклатура операций, Ксп = 20-5-40 операций (/Ссер > 20; Км < 1). Оборудование, виды движений, формы специализации и производственная структура те же, что и при единичном производстве. Для среднесерийного производства характерно, что выпуск изделий производится довольно крупными сериями ограничен¬ной номенклатуры; серии повторяются с известной регуляр¬ностью по периоду запуска и числу изделий в партии; годичная номенклатура все же шире, чем номенклатура выпуска в каждом месяце. За рабочими местами закреплена более узкая номенклатура операций, Ксп — 10 -*• 20 опера¬ций (Keep -20; Кы < 1). Оборудование универсальное и специ¬альное, вид движения предметов труда — параллельно-после¬довательный. Заводы имеют развитую производственную структуру, заготовительные цехи специализируются по техно¬логическому принципу, а в механосборочных цехах создаются предметно-замкнутые участки. Крупносерийное производство тяготеет к массовому. Из¬делия производятся крупными сериями ограниченной номен¬клатуры, а основные или важнейшие выпускаются постоянно и непрерывно. Рабочие места имеют более узкую специализа-цию, /Соп = 2 -н 10 операций (/Ссер = 10; Км < 1). Оборудование преимущественно специальное, виды движений предметов труда — параллельно-последовательный и параллельный. За¬воды имеют простую производственную структуру, обрабаты-вающие и сборочные цехи специализированы по предметному принципу, а заготовительные — по технологическому. Массовое производство характеризуется выпуском узкой номенклатуры изделий в течение длительного периода време¬ни и большим объемом, стабильной повторяемостью. За рабо¬чими местами закреплена узкая номенклатура операций, Ксп < 1 операции (/Ссер < 2; Км s 1). Все изделия номенклатуры завода изготовляются одновременно и параллельно. Числа наимено¬ваний изделий в годовой и месячной программах совпадают. Оборудование специальное, вид движения предметов труда -параллельный. Цехи и участки специализированы преимуще¬ственно по предметному принципу. Заводы имеют простую и четко определенную производственную структуру. В сочетании механизации и автоматизации производствен¬ных процессов, атакже загрузки рабочих мест (оборудования) с видами движений предметов труда можно получить серий¬ное производство в четырех и массовое производство в трех вариантах (рис. 4.3). Исходя из типа производства устанавливается тип пред¬приятия и его подразделений. На каждом предприятии могут существовать различные типы производства. Поэтому тип предприятия или его подразделения определяется по преоб¬ладающему на нем типу конечного производства.11. Методы обработки со снятием материала
Обработка со снятием материала – это, в первую очередь, обработка металла резанием со снятием стружки. Она позволяет придать деталям желаемую форму. Формообразование при обработке резанием обеспечивается за счет снятия стружки при перемещении инструмента и обрабатываемой детали. Преимуществами этого способа обработки являются широкая сфера применения и высокая точность. Кроме других способов, механическая обработка резанием включает в себя токарную и фрезерную обработку и сверление. Методы следа, копирования и огибания. Они определяются формой главного движения, движения подачи и формой режущей кромки. Поверхность, обрабатываемая методом следа, образуется вершиной режущей кромки в соответствии с формой траектории движения подачи. При формообразовании методом копирования поверхность (профиль) заготовки образуется одновременно всеми точками режущей кромки, т.е.копируется. При формообразовании методом огибания требуемая поверхность заготовки образуется точкой (или участком) режущей кромки, перемещающейся по поверхности в процессе обработки за счет кинематики процесса обработки (согласованных перемещений инструмента и заготовки: винтообразных, обкатных и др.).12. Взаимосвязь технологичности конструкции технологии сборки изделия.
Взаимосвязь конструкции изделия с технологией его производства обусловила одну из наиболее сложных функций технологически подготовки производства — отработку конструкции изделия н технологичность. Недостаточно полное и четкое выполнение этой функции на практике является причиной изготовления в промышленности неотработанных на технологичность изделий, что вызывает неоправданные затраты труда, средств, материалов и времени. На отдельных предприятиях различных отраслей промышленности производится отработка конструкции изделия на технологичность, но методы отработки обычно существенно различаются. Отсутствие единой методики отработки конструкций на технологичность затрудняет сравнительную оценку технологичности изделий и обмен опытом создания технологичных изделий. Обязательность отработки конструкций изделий на технологичность на всех стадиях их создания устанавливается стандартами ЕСТПЛ. Совершенство конструкции машины характеризуется ее соответствием современному уровню техники, экономичностью и удобством в эксплуатации, а также тем, в какой мере учтены возможности использования наиболее экономичных и производительных технологических методов ее изготовления применительно к заданному выпуску и условиям производства. Конструкцию машины, в которой эти возможности полностью учтены, называют технологичной. Таким образом, технологичность конструкции изделий (ТКИ) — это совокупность таких свойств конструкции изделия, которые определяют ее приспособленность к достижению оптимальных затрат при производстве, эксплуатации и ремонте для заданных показателей качества, объема выпуска и условий выполнения работ. Отсюда следует, что ТКИ — понятие относительное. Технологичность одного и того же изделия в зависимости от тина производства, где оно изготавливается, и от конкретных производственных условий может быть, различной. ТКИ — понятие комплексное. Ее нельзя рассматривать изолированно, без взаимной связи и учета условий выполнения заготовительных процессов, процессов обработки, сборки и контроля, ремонта и эксплуатации. Улучшением технологичности конструкции можно увеличить выпуск продукции при тех же средствах производства. Трудоемкость машин нередко удается сократить на 15-25% и более, а себестоимость их изготовления на 5-10%. Основная задача обеспечения ТКИ заключается в достижении оптимальных трудовых, материальных и топливно-энергетических затрат на проектирование, подготовку производства, изготовление, монтаж вне предприятия-изготовителя, технологическое и техническое обслуживание, ремонт при обеспечении прочих заданных показателей качества изделия в принятых условиях проведения работ. Главными факторами, определяющими требования к ТКИ, являются: · вид изделия, степень его надежности и сложности, условия изготовления, технического ремонта и обслуживания, показатели качества; · тип производства; · условия производства, в том числе наличие передового опыта и прогрессивных методов изготовления аналогичных изделий, оборудования, оснастки и т. д.13. Технологический переход, установ, позиция, рабочий ход
Технологическая операция – законченная часть технологического процесса, выполняемая на одном рабочем месте. Установ– часть технологической операции, выполняемая при неизменном закреплении обрабатываемых заготовок или собираемой сборочной единицы. Технологический переход – законченная часть технологической операции, выполняемая одними и теми же средствами технологического оснащения при постоянных технологических режимах и установке. Применительно к механической обработке определение перехода можно уточнить следующей формулировкой:технологический переход представляет собой законченную часть технологической операции, выполняемую над одной или несколькими поверхностями заготовки, одним или несколькими одновременно работающими инструментами, без изменения или при автоматическом изменении режимов работы станка. Элементарный переход –часть технологического перехода, выполняемая одним инструментом над одним участком поверхности обрабатываемой заготовки за один рабочий ход без изменения режимов работы станка. Вспомогательный переход– законченная часть технологической операции, состоящей из действий человека и (или) оборудования, которые не сопровождаются изменением свойств предметов труда, но необходимы для выполнения технологического перехода (закрепление заготовки, смена инструмента и т.д.). Позиция – фиксированное положение, занимаемое неизменно закрепленной обрабатываемой заготовкой или собираемой сборочной единицей совместно с приспособлением относительно инструмента или неподвижной части оборудования при выполнении определенной части операции. Рабочий ход – часть технологического перехода, состоящая из однократного перемещения инструмента относительно заготовки, сопровождаемого изменением формы, размеров, качества поверхности, свойств заготовки. Вспомогательный ход – часть технологического перехода, состоящая из однократного перемещения инструмента относительно заготовки, необходимого для подготовки рабочего хода. Наладка – подготовка технологического оборудования и технологической оснастки к выполнению технологической операции.14. Методика разработки технологического маршрута обработки поверхности детали в целом.
Маршрут обработки поверхности (МОП) – это последовательность методов (видов, переходов одного метода) обработки, необходимых для достижения требуемых чертежом детали параметров поверхности. Такими параметрами являются: -геометрический тип поверхности; -точность размера; -шероховатость; -вид термообработки и т.д. Определение последовательности технологических операций Общая схема технологического процесса изготовления детали может быть представлена в виде последовательных приближений к показателям детали в соответствии с требованиями чертежа. Этапы приближения: операции 1-го приближения (заготовительные); операции 2-го приближения (черновая обработка); операции 3-го приближения (чистовая обработка); операции 4-го приближения (отделочные работы). Подобный методический подход объясняется тем, что на стадии черновой обработки появляются сравнительно большие погрешности, вызываемые деформациями, возникающими в процессе резания, а также значительным нагревом заготовки. Кроме того, вынесением отделочных операций в конец маршрута уменьшают риск случайного повреждения окончательно обработанных поверхностей в процессе транспортировки. Также учитывается то, что черновую обработку могут выполнять рабочие более низкой квалификации на изношенном оборудовании. При установлении общей последовательности обработки сначала обрабатывают поверхности, принятые за технологические базы. Затем обрабатывают остальные поверхности в последовательности, обратной степени их точности. Изложенный принцип построения маршрута, однако, не во всех случаях обязателен. При жесткой заготовке и малых размерах обрабатываемых поверхностей окончательную обработку отдельных элементов можно выполнять и в начале маршрута. Если деталь подвергают термической обработке, то технологический процесс изготовления детали расчленяют на две части: до термообработки и после нее. Для устранения возможных деформаций часто приходится предусматривать правку деталей или обработку отдельных поверхностей после термообработки, Последовательность обработки зависит от назначенных конструкторских баз. После операции механообработки, как правило, назначают контрольную операцию. Последовательность операций также может измениться, если деталь обрабатывается по типовому или групповому процессу. Составление технологического маршрута обработки детали предшествует оформлению технологического процесса на картах и ведется в черновой тетради, с последующим изложением в пояснительной записке (для курсовых проектов). При разработке двух или нескольких вариантов маршрутов (изготовление детали из разных заготовок, на разном оборудовании и т.п.) выбирается наиболее экономичный в данных производственных условиях. Если его определить затруднительно, то проводится соответствующий экономический расчет. В маршрут включаются все операции. Технологический маршрут изготовления детали, утвержденный руководителем, служит основанием для разработки технологического процесса на операционных картах.15. Проектирование технологических процессов сборки изделий.
Технологическая подготовка сборочного производства состоит из разработки технологического процессов проектирования и изготовления специальной оснастки, нестандартного оборудования, выполнения необходимых расчётов, планировок и других работ. Наиболее важной частью технологической подготовки сборочного производства является проектирование технологического процесса сборки. Технологическая операция сборки представляет собой законченную часть процесса сборки, выполняемого непрерывно над одной сборочной единицей или над совокупностью одновременно собираемых единиц одним или группой рабочих на одном рабочем месте. Сборочная операция – это технологическая операция установки и образования соединений составных частей изделия. При некоторых организационных формах сборки сборочный процесс может в явной форме на операции и не расчленяться. Содержание операции и переходов технологического процесса сборки определяется конструкцией изделия, совершенством технологии механической обработки детали, организационно-техническими условиями сборочного производства и размерами производственного задания. Одной из важных задач разработки технологического процесса является выбор степени его расчленённости (дифференциации). Концентрированный процесс сборки характерен для единичного опытного или мелкосерийного производства (одно или несколько рабочих мест). Если изделие включает типовые сборочные элементы, то узловая сборка дифференцируется, а общая – ведётся концентрировано. Недостатками концентрированной сборки являются: длительность календарного цикла вследствие последовательного выполнения операций, невозможность выделения отдельных работ, трудоёмкость механизации автоматизации работ. Дифференциация технологических процессов сборки характерно для устойчивого мелкосерийного, а также, для серийного и массового производства. Она позволяет расчленить процесс на операции, время которых связано с тактом и обеспечивает в пределах одной квалификации одинаковые работы. Это создаёт предпосылки для автоматизации и механизации. Степень автоматизации зависит не только от объёма производства, но и от конструкции изделия, его характерных размеров и числа деталей. Технологический процесс сборки разрабатывается в следующей последовательности: 1. В зависимости от программного задания устанавливается целесообразная организационная форма сборки. 2. Производится технологический анализ сборочных чертежей и рабочих чертежей деталей с целью отработки технологичности конструкции. 3. Производится размерный анализ конструкции с выполнением соответствующих расчётов и устанавливаются рациональные методы обеспечения требуемой точности сборки. Определяется вероятное количество деталей и узлов пригодных для взаимозаменяемой сборки по методу неполной взаимозаменяемости. Определяются размеры регулирования и пригонки. 4. Определяется целесообразная в данных условиях производства степень дифференциации проектируемого процесса сборки. 5. Устанавливается последовательность соединения всех сборочных единиц и деталей изделия и составляются схемы общей сборки и узловых сборок изделия. Устанавливается схема сборочного состава и составляется технологическая схема сборки. 6. Определяются наиболее рациональные способы соединения, проверки положения и фиксации всех составляющих сборочных единиц и изделий. Составляется содержание технологических операций и задаются методы контроля и окончательных испытаний изделия. 7. Подбор оборудования. 8. Разработка необходимой технической оснастки – приспособления, режущий и контрольно-измерительный инструмент. 9. Производится техническое нормирование сборочных работ и рассчитываются технологические показатели процесса сборки (определение разряда работы, выбор режима выполнения операций и т.д.). 10. Оформление технологической документации процесса сборки. Кроме этого, производится разработка системы контроля, определяются трудозатраты и расход материалов, а затем осваивается технологический процесс.16. Технологическая схема сборки
Изучение собираемого изделия завершается составлением технологических схем общей и узловой сборки.Эти схемы в наглядной форме отражают маршрут сборки изделия, его составных частей. Элементы, снимаемые в неразборном виде, представляют собой части изделия, на которые далее составляют технологические схемы узловой сборки. Если изделие имеет несколько размерных цепей, то сборку необходимо начинать с наиболее сложной и ответственной. При наличии размерных цепей с общими звеньями начинают сборку с элемента той цепи, которая влияет в большей степени на точность изделия. На последовательность сборки влияет взаимозаменяемость, конструирования базовых элементов, условия монтажа, постановка легко повреждаемых элементов в конце сборки, размеры и масса присоединяемых элементов. При производстве не взаимозаменяемых элементов на последовательность сборки влияют пригоночные, промежуточные разработка и сборка изделия детали. Технологические схемы узловой сборки разрабатывается в этом случае параллельно, что сокращает время на подготовку производства. Вариант схемы сборки выбирают с учетом удобства и контроля качества сборки, числа сборщиков и др. Применяемый вариант схемы на последующих этапах м.б. скорректирован с учетом необходимой догрузки сборщиков на отдельных постах. 17. Обоснование схем базирования при механической обработке корпусных деталей на первом и последующих операциях Чаще всего в качестве базовых выбирают те поверхности КД, относительно которых на рабочем чертеже детали закоординировано большее число поверхностей. 1) Базирование по плоскости и двум взаимно перпендикулярным отверстиям по отношению к базовой плоскости. Широко применяется в массовом производстве. Деталь устанавливается на базовую плоскость 1, цилиндрическую 3 и срезанный палец 4, которые входят в базовые отверстия 2. Базовые отверстия разворачиваются до 8 квалитета (эти отверстия – искусственные базы). КД устанавливают на пальцы с гарантированным зазором 0,02мм. (Блоки, головки – призматического типа). «+»: простота конструкции приспособления: плита и два штыря пальца; заготовка открыта для обработки практически со всех сторон, т.е. высокая доступность режущего инструмента к обрабатываемой поверхности. Применяется в условиях автоматического производства. «-»: не высокая точность за счёт зазоров. Приспособление очень габаритно за счёт необходимости разнесения пальцев. 2) Базирование КД фланцевого типа. Деталь устанавливается на плоскость фланца 1, выточку большого диаметра 2 во фланце и на отверстие малого диаметра 3, в которое входит ромбический палец 4. Установка похожа на предыдущую схему. 3) Установка заготовок на 6 точек. Применяется для установки крупных корпусных деталей. Заготовка лишается всех 6 степеней свободы (коорд. угол). «+»: универсальность; высокая точность установки. «-»: резко уменьшается доступ к обрабатываемым поверхностям (направляющая и опорная базы ограничены); трудно выдерживать принцип постоянства баз. 4) Базирование деталей станков. Установочный элемент выпуклый. Базирование происходит по поверхностям 1 и 2 (лишается 5 степеней свободы). 6 степень убирается.3 – упор устанавливается с противоположной стороны базы. 5) Базирование КД типа тел вращения.18. Методы обработки зубьев колес
Выбор метода обработки зубчатых колес находится в непосредственной зависимости от установленной нормы точности различных их элементов, а также от основных требований к передачам в процессе их эксплуатации. С этой точки зрения зубчатые передачи можно разбить на следующие группы: силовые передачи больших мощностей и высоких скоростей; основное требование – обеспечение высоких КПД; силовые промышленные и транспортные передачи при средних скоростях; требования – надежность и плавный ход; силовые передачи в станкостроении; требования – постоянство передаточного отношения и плавность хода; переачи в автомобилестроении; требования – плавность и легкость хода, отсутствие шума; кинематические передачи в точных приборах; требования – обеспечение постоянства передаточных отношений, отсутствие мертвого хода. Установленные ГОСТом степени точности учитывают эти условия, допуская высокие технические показатели в одном направлении и низкие в другом. Зубчатые колеса обрабатывают на разнообразных зубообрабатывающих станках. Зубья на колесах нарезают двумя способами: копированием и обкаткой. При копировании режущему инструменту придают форму впадины между зубьями, а затем производят обработку. При этом профиль инструмента копируется на обрабатываемой поверхности. Зубонарезание способом копирования можно выполнять: последовательным нарезанием каждого зуба колеса модульной дисковой или пальцевой фрезой на универсальном фрезерном станке; одновременным долблением всех зубьев колеса; одновременным протягиванием всех зубьев колеса; круговым протягиванием. Способ копирования применяется главным образом при изготовлении зубчатых колес невысокой точности. Современным, точным и производительным способом изготовления зубчатых колес является нарезание зубьев по способу обкатки червячной фрезой, круглым долбя ком, реечным долбяком (гребенкой), зубострогальными резцами, резцовой головкой, накатыванием зубчатыми валками. Способ обкатки заключается в том, что зубья на зубчатом колесе образуются при совместном согласованном вращении (обкатке) режущего инструмента и заготовки. Так, при зубофрезеровании прямолинейные боковые режущие кромки зубьев червячной фрезы, имеющие в осевом сечении трапецеидальную форму, поочередно касаются нарезаемого зуба. Рассматривая последовательные положения зубьев фрезы (1, 2, 3 и т.д.), видим, что профиль впадины получается постепенно и состоит из множества прямолинейных участков, образованных зубьями фрезы. Эти прямолинейные участки накладываются один на другой и практически образуют не ломаный, а криволинейный (эвольвентный) профиль зуба. Зубчатые колеса 3…8-й степеней точности нарезают методом обкатки. Сырые колеса 3…5-й степеней точности далее подвергают тщательной обработке шевингованием, шлифованием и последующей отделке на притирочных станках, после чего их закаливают токами высокой частоты (ТВЧ), исключающими деформацию поверхности. Зубчатые колеса, изготовленные по 6…8-й степеням точности, обычно подвергают закалке в закалочных печах, дающих значительное искажение формы. Затем для сохранения формы у колес с б-й и 7-й степенями точности шлифуют боковые профили зубьев с базированием по отверстию, а у колес с 8-й степенью точности шлифуют отверстие с базированием по впадине зуба. Зубчатые колеса, изготовляемые по 8…10-й степеням точности, нарезают в мелкосерийном производстве на фрезерных станках в делительной головке, причем для колес, изготовляемых с 8-й степенью точности, фрезы тщательно-профилируют по форме зубьев колеса. Зубчатые колеса с 10-й и 11-й степенями точности могут быть получены точной отливкой с последующей обработкой зубьев по шаблону 19. Винтовые и эксцентриковые зажимные механизмы приспособлений Винтовые ручные зажимы находят большое применение в станочных приспособлениях вслед¬ствие их простоты и надежного закрепления заготовок- Не-достатки винтовых зажимов: значительное вспомогательное время, необходимое для разжима и зажима детали, больно затрата рабочим мускульной силы, непостоянство силы за¬жима и возможность смешения заготовки от силы трения на торце винта. Винтовые зажимы применяют при ручном закреплении заготовок в приспособлениях, а также в приспособлениях механизированного типа и при зажиме заготовок в приспособлениях — спутниках, применяемых для деталей, изготав-ливаемых на автоматических линиях. Закрепление заготовок винтовыми зажимами в приспо¬соблениях производится ключами, ручками, гайками, гай¬ками-головками, установленными на конце винта. Зажим¬ные винты и гайки изготовляют из стали 35 и 45 с твердо¬стью HRC 30-35 и точностью резьбы по 3-му классу. Сила, с которой зажимают заготовку винтовым зажи¬мом, зависит от длины рукоятки и величины приложенной к ней силы, формы зажимного торца и вида резьбы. . Момент от силы Q, приложенной на рукоятке резьбового зажима со сферическим зажимом: Эксцентриковые зажимы являются быст¬родействующими, но развивают меньшую силу зажима; чем винтовые, имеют ограниченное линейное перемещение и не могут надежно работать при значительных колебаниях раз¬меров между установочной и зажимаемой поверхностями обрабатываемых заготовок данной партии. В приспособле¬ниях применяют круглые и криволинейные эксцентриковые зажимы. Круглый эксцентриковый зажим представляет со¬бой диск или валик, поворачиваемый вокруг оси, смещенной относительно геометрической оси эксцен-трика на некоторую величину, называемую эксцентриси¬тетом. Для надежного закрепления заготовок эксцентрико¬вые зажимы должны быть самотормозящимися. Круглые эксцентрики изготовляют из стали 20Х, цемен¬тируют на глубину 0,8-1,2 мм и затем закали¬вают до твердости HRC 55-60; некоторые виды круглых эксцентриков нормализованы. Из тео¬ретической механики известно, что условие самоторможения двух трущихся тел определя¬ется: , где — угол трения; — угол подъе¬ма, под которым проис¬ходит трение. Следова¬тельно, если угол подъ¬ема эксцентрика в определенном его по¬ложении не больше угла трения , то эксцентрик является самотормозящимся. Самотормозящиеся эксцен¬трики после зажима заготовки не изменяют своего положе¬ния. Самоторможение эксцентриковых зажимов обеспечивается при определенном отношении его наружного диаметра D к эксцентриситету «е». Стандартные круглые эксцентрики имеют размеры D=32-70 мм и е= 1,7-3,5 мм. Следовательно, круглые экс¬центрики имеют небольшой линейный ход и их не следует применять для зажима заготовок деталей, имеющих боль¬шой допуск на размер детали в направлении ее зажима. Достоинство круглых эксцентриков — простота их изго¬товления; недостатки — изменение угла подъема а и силы зажима W при закреплении заготовок с большими колеба¬ниями размеров в направлении зажима. Криволиней¬ные эксцентрики при сравнении с круглыми имеют сле¬дующие преимущества: 1. Большой угол поворота эксцентрика (100-150°); 2. Более постоянную силу зажима обрабатываемых де¬талей. Сила зажима экс¬центриковым прихва¬том в 5-4 раза меньше, чем резьбовым при одинаковых длине ру¬коятки и исходной силе.21. Методы производства заготовок ступенчатых валов и особенности их механической обработки
Существуют три основных метода обработки ступенчатых валов на универсальных токарных станках: 1)без применения специального технологического оснащения; 2)на настроенных станках с применением специального технологического оснащения; 3)на станках, оснащенных устройствами или суппортами для копировальной обработки 1. Как правило, токарная обработка ступенчатых валов производится не менее чем за две установки. При благоприятных условиях, когда ведется обтачивание под шлифование жестких ступенчатых валов нормальной точности из хорошо выправленных и зацентрованных заготовок при небольших припусках, вполне можно обойтись только двумя установками. При этом за первую установку полностью обрабатывается один конец вала, а за вторую другой. Токарная обработка валов с повышенной точностью, а также изготовляемых из заготовок с большими неравномерными припусками, производится за три-четыре установки. При четырех установках за первые две установки производится черновая обработка вала, а за две последние чистовая. Во время чистовой обработки устраняются искривления оси вала, появившиеся в результате перераспределения внутренних напряжений в материале после обдирки. В отдельных случаях, главным образом при обработке ступенчатых валов несимметричной формы, обтачивание их может быть выполнено за три установки: за первые две установки производится черновая обработка вала и чистовая обработка его длинной части; за третью установку окончательно обтачивается короткая часть вала. При разделении токарной обработки валов на самостоятельные черновые и чистовые операции необходимо между черновой и чистовой операциями дать возможность валам некоторое время вылежаться для уравновешивания возникших в заготовке внутренних напряжений. 1 На заводах крупносерийного н массового производства ступенчатые валы обрабатываются на многорезцовых станках автоматического и полуавтоматического действия. Большое значение имеет также правильный выбор места вала, с которого следует начать обработку. В этом случае руководствуются следующими соображениями: 1)если вал более или менее симметричен и разница в диаметрах шеек на разных его концах сравнительно невелика, то обработка такого вала может быть начата с любого конца; 2)при значительной разнице в диаметрах ступеней на разных концах вала обработку его следует начинать с более толстого конца; этим уменьшается опасность искривления вала при обработке его второго конца; 3)если обе концевые шейки вала тонкие, то окончательное их обтачивание следует выполнять после обработки всех остальных ступеней. Обработка ступенчатых валов на универсально-токарных станках (без специальной настройки). Этот метод по сравнению с другими методами обработки этих же валов является наименее производительным и выполняется рабочими высокой квалификации. Установка резцов на размер (по диаметру и по длине) при таком методе работы в большинстве случаев осуществляется путем пробных проходов и измерений универсальными инструментами и только в отдельных случаях для установки резцов на заданные размеры используются имеющиеся на станках лимбы и универсальные упоры. Такой способ обработки ступенчатых валов применяется в единичном и мелкосерийном производстве, когда расходы на изготовление технологической оснастки и на предварительную настройку станка не окупаются достигаемым повышением производительности труда. Обработка ступенчатых валов на настроенных токарных станках. Применение для изготовления ступенчатых валов высокопроизводительных специальных станков является рациональным лишь в серийном и массовом производстве. В условиях мелкосерийного производства для обработки ступенчатых валов применяются обычные универсальные токарные станки. Наиболее рациональным методом работы на универсальных станках в серийном производстве является работа на настроенных станках, т. е. на станках, специально подготовленных для выполнения определенной технологической операции. Производительность обработки детали на заранее настроенном станке значительно выше, чем на обычном станке. Это объясняется тем, что благодаря оснащению станка специальными приспособлениями отпадает надобность в пробных проходах и измерениях, появляется возможность сокращения времени на установку деталей и т. д. Предварительная настройка универсального токарного станка для выполнения той или иной технологической операции по обработке ступенчатого вала предусматривает: 1)оснащение станка надежными и быстродействующими приспособлениями для установки и крепления обрабатываемой детали; 2)подготовку необходимых инструментов и установление рационального режима резания для обработки отдельных поверхностей вала; 3)оснащение станка необходимыми приспособлениями и устройствами для облегчения или автоматизации установки резцов и обеспечения заданных диаметральных и- линейных размеров отдельных ступеней обрабатываемого вала; 4)наличие подготовленного заранее комплекта инструментов, устанавливаемого взамен затупившихся инструментов. Наибольшее влияние на продолжительность обработки вала оказывает принятое количество и расположение резцов. В зависимости от количества и расположения резцов, а также от количества, конструкции и расположения резцедержателей для их крепления, различают следующие три основные схемы обработки ступенчатых валов на настроенных универсальных токарных станках: 1)с использованием только одного поворотного (четырехгранного) резцедержателя; 2)с использованием, кроме основного универсального поворотного резцедержателя, также специальных дополнительных резцедержателей; 3)с применением специальных многорезцовых резцедержателей. Обработка ступенчатых валов при использовании только одного поворотного резцедержателя. При такой настройке токарного станка все резцы, необходимые для выполнения заданной операции, устанавливаются в четырехгранном поворотном резцедержателе. Расположение резцов в резцедержателе при этом согласовывается с принятой последовательностью обработки отдельных поверхностей вала.22. Вакуумные и электромагнитные приспособления
Вакуумные приводы приспособле¬ний применяют для непосредственной передачи атмосфер¬ного давления на закрепляемую заготовку. В приспособле¬ниях с вакуумным зажимом между базовой поверхностью заготовки и полостью приспособления создается разрежение — вакуум и обраба¬тываемая заготовка прижимается к опо¬рным поверхностям приспособления из¬быточным атмос¬ферным давлением. Приспособления с вакуумным зажимом применяют при чис¬товой обработке за¬готовок нежестких деталей, которые мо¬гут деформироваться при приложении сил зажима на неболь¬ших поверхностях. Управление вакуумным приспособлением производится четырехходовыми или трехходовым краном, который под¬ключает вакуумное приспособление к пневмоцилиндру или к насосу или соединяет вакуумную полость приспособления с атмосферой. Сила зажима заготовки в вакуумном приспо¬соблении контролируется ртутным манометром. Вакуумные приспособления применяют для крепления заготовок тонких пластинчатых деталей при чистовой об¬работке. В станочных приспособлениях с электромагнитным приводом рабочий магнитный поток, создавае¬мый электромагнитными катушками или постоянными маг-нитами, образует силу, которая производит крепление заго¬товки на плоскости магнитного приспособления. Электромагнитные приводы встраивают в плиты, па¬троны, на верхней плоскости которых обработанной по¬верхностью устанавливают детали. Питание электромагнит¬ных плит производится постоянным током от моторгенераторов или селеновых выпрямителей. Сила зажима заготовки на электромагнитной плите за¬висит от удельного притяжения плиты, габаритных размеров детали и ее размещения на столе; она возрастает до опреде¬ленной величины с увеличением толщины и площади попе-речного сечения заготовки. С увеличением шероховатости базовой поверхности заготовки сила зажима уменьшается. Для надежного закрепления заготовка на электромагнитной плите должна перекрыть два соседних участка, расположен¬ных между двумя смежными вставками. Недостатки электромагнитных приводов приспособлений: получение меньшей силы зажима деталей по сравнению с механизированными приводами; на них нельзя крепить заготовки из немагнитных мате¬риалов. Электромагнитные плиты и патроны при¬меняют для установки и закрепления заготовок, обрабаты¬ваемых шлифованием, чистовым фрезерованием, точением.23. Обоснование схем базирования при механической обработке деталей класса «полые цилиндры» на первой и последующих операциях
Особенности механической обработки деталей класса III рассмотрим на примере весьма ответственных и сложных по технологии изготовления – поршней двигателей. Поршни изготавливают в большинстве случаев из алюминиевых жаростойких сплавов марок АЛ-30, АК 18, АК 21, ВКЖЛС-2, АК10М2Н и др. Отливка заготовок производится в металлические разборные формы (кокиль). После отливки заготовки подвергаются термической обработке по режиму Т1 (искусственное старение). Механическая обработка поршней сложна строгие требования к обеспечению точности размеров, правильности взаимного расположения рабочих поверхностей – отверстий под палец по отношению к поверхности головки и юбки. Обычно в качестве чистовых установочных баз используют вспомогательные базы, а именно: подрезанный открытый торец и внутреннюю выточку с открытого торца. При обработке чистовых вспомогательных баз со стороны открытого торца поршни устанавливают обычно по наружной поверхности их головки и днищу, которые в этом случае являются черновыми установочными базами.24. Производство заготовок и особенности механической обработки блока цилиндров ДВС или картера КПП автомобиля
Для блока цилиндров ДВС выберем литье по выплавляемым моделям. Применяется в случаях изготовления деталей высокой точности (например лопатки турбин и т. п.) Из легкоплавкого материала: парафин, стеарин и др., (в простейшем случае — из воска) изготавливается точная модель изделия и литниковая система. Наиболее широкое применение нашёл модельный состав П50С50 состоящий из 50 % стеарина и 50 % парафина, для крупногабаритных изделий применяются солевые составы менее склонные к короблению. Затем модель окунается в жидкую суспензию на основе связующего и огнеупорного наполнителя. В качестве связующего применяют гидролизованный этилсиликат марок ЭТС 32 и ЭТС 40, гидролиз ведут в растворе кислоты, воды и растворителя (спирт, ацетон). В настоящее время в ЛВМ нашли применения кремнезоли не нуждающиеся в гидролизе в цеховых условиях и являющиеся экологически безопасными. В качестве огнеупорного наполнителя применяют: электрокорунд, дистенсилиманит, кварц и т. д. На модельный блок (модель и ЛПС) наносят суспензию и производят обсыпку, так наносят от 6 до 10 слоёв. С каждым последующим слоем фракция зерна обсыпки меняются для формирования плотной поверхности оболочковой формы. Сушка каждого слоя занимает не менее получаса, для ускорения процесса используют специальные сушильные шкафы, в которые закачивается аммиачный газ. Из сформировавшейся оболочки выплавляют модельный состав: в воде, в модельном составе, выжиганием, паром высокого давления. После сушки и вытопки блок прокаливают при температуре примерно 1000 для удаления из оболочковой формы веществ способных к газообразованию. После чего оболочки поступают на заливку. Перед заливкой блоки нагревают в печах до 1000. Нагретый блок устанавливают в печь и разогретый металл заливают в оболочку. Залитый блок охлаждают в термостате или на воздухе. Когда блок полностью охладится его отправляют на выбивку. Ударами молота по литниковой чаше производится отбивка керамики, далее отрезка ЛПС.Таким образом получаем отливку. Преимущества этого способа: возможность изготовления деталей из сплавов, не поддающихся механической обработке; получение отливок с точностью размеров до 11 — 13 квалитета и шероховатостью поверхности Ra 2,5-1,25 мкм, что в ряде случаев устраняет обработку резанием; возможность получения узлов машин, которые при обычных способах литья пришлось бы собирать из отдельных деталей. Литье по выплавляемым моделям используют в условиях единичного (опытного), серийного и массового производства. В силу большого расхода металла и дороговизны процесса ЛВМ применяют только для ответственных деталей. Процесс литья по выплавляемым моделям базируется на следующем основном принципе: Копия или модель конечного изделия изготавливаются из легкоплавкого материала. Эта модель окружается керамической массой, которая затвердевает и образует форму. При последующем нагревании (прокалке) формы модель отливки расплавляется и удаляется. Затем в оставшуюся на месте удалённого воска полость заливается металл, который точно воспроизводит исходную модель отливки. Фрезерование (фрезерная обработка) — обработка материалов резанием с помощью фрезы. Фреза совершает вращательное, а заготовка — преимущественно поступательное движение. В процессе фрезерования участвуют два объекта — фреза и заготовка. Заготовка — это будущая деталь. В данном случае так как нам нужна расточка, сверление отверстий то используем концевое фрезерование. Финишная обработка блока цилиндров — фрезеровка наружной поверхности, сверление и расточка отверстий. Для обеспечения точности, блока обрабатываются за минимальное число переустановок. Процесс полностью автоматизирован — программа управления станками отдает последовательные команды роботу. Из процесса финишной обработки головки цилиндров человек исключен.25. Разновидности и особенности клино-плужерных силовых механизмов
Клиноплунжерные оправки широко применяются на токарных, шлифовальных и зубообрабатывающих станках. По исполнению бывают шпиндельные и фланцевые. Шпиндельные оправки непосредственно встраиваются в шпиндель станка и предназначены для обработки мелких деталей с установочным отверстием порядка 10-30 мм. На рисунке 2.23 показана схема фланцевой оправки, которая фланцем корпуса крепится на планшайбе станка. В равномерно расположенных по окружности корпуса 1 в радиальных пазах устанавливаются плунжеры 2. Внутри корпуса располагается клиновая втулка 3. Втулка по периферии имеет клиновые пазы. Каждый плунжер контактирует со своим клиновым пазом. Количество плунжеров и пазов z=3-6. Втулка имеет центральные отверстия для крепления со штоком привода 5. Во время установки заготовки исходная сила привода прикладывается к втулке. Под действием исходной силы втулка перемещается вдоль оси оправки в направлении исходной силыW, при этом плунжеры получают синхронные радиальные перемещения от оси к заготовке. Таким образом происходит центрирование и закрепление заготовки. После снятия исходного усилия втулка принимает исходное положение под действием центральной пружины (на рис. не показана), а плунжеры под действием кольцевой разрезной пружины 4. При расчете полагают что радиальная сила зажима Q на оси оправки взаимно уравновешивается и практически сила трения между втулкой и корпусом отсутствует, поэтому расчетное уравнение для клиноплунжерных оправок выглядит следующим образом. Установка на клиноплунжерные оправки проста по исполнению, легко автоматизируется и может выполняться с установочным кольцом. В этом случае плунжеры воздействуют на заготовку через тонкостенное разрезное кольцо. Такие оправки обеспечивают равномерное распределение силы зажима по установочному отверстию заготовки и применяются при обработке деталей с низкой радиальной жесткостью, а также когда установка выполняется по чисто обработанному отверстию, однако, в этом случае часть исходного усилия затрачивается на деформацию втулки и запас хода ограничивается ее упругими свойствами. Оправки без установочного кольца имеют сравнительно большой диаметральный ход плунжеров (до 10 мм) при α=6.110, обеспечивает большие силы зажима, что позволяет их использовать для установки по чистовым и предварительно обработанным отверстиям. В зависимости от длины установочного отверстия применяются оправки с одним или двумя рядами плунжеров. Однорядные оправки (рис. 2.23) применяются, когда длина отверстия меньше его диаметра или соизмерима с ним. В этом случае технологическими базами является Т1 – торец заготовки, установочная явная база, Т2 – ось заготовки, двойная опорная скрытая база, реализуется путем центрирования заготовки на оправке.26. Влияние параметров шероховатости на эксплуатационных показатели изделий
В процессе выполнения любого способа обработки деталей, особенно со снятием материала режущим инструментом, невозможно получить идеально ровную поверхность. В результате вибраций, неровностей обрабатываемого инструмента, неоднородности материала заготовки, непостоянства скорости съема материала и подачи на обрабатываемой поверхности остаются неровности. Поверхностные неровности влияют на следующие эксплуатационные свойства элементов детали. 1.При образовании посадок с натягом, чем больше поверхностные неровности, тем менее надежным оказывается сопряжение, поскольку уменьшается площадь контакта, даже при идеальной геометрической форме элементов деталей. 2.При образовании посадок с зазором большие поверхностные неровности быстро истираются и в результате увеличивается первоначальный зазор. При истирании частицы материала не всегда удаляются полностью из сопряжения и могут способствовать ускоренному износу поверхностей. Поэтому для многих механизмов, и в частности, для двигателей автомашины, устанавливают ограничения по нагрузке в начальный период эксплуатации и через определенный срок работы требуется смена смазки для того, чтобы удалить продукты износа из механизма. Часто при этом используется термин «приработка», т.е. время работы, в основном, для «сглаживания» поверхностных неровностей. 3.Поверхностные неровности влияют на усталостную прочность. Излом элементов деталей обычно бывает в местах, где имеются риски, особенно если деталь работает при знакопеременной нагрузке. 4.Поверхностные неровности влияют на антикоррозийные свойства поверхности. Чем меньше поверхностные неровности, тем меньше коррозии появляются на поверхности. Чем больше поверхностные неровности, тем больше представляется возможным накопление в неровностях влаги и кислот, находящихся в окружающей среде, что способствует распространению коррозии. 5.Поверхностные неровности влияют также на качество электрических и тепловых контактов, герметичность соединений, отражение лучей, точности измерений, особенно внутренних размеров и т.д27. Методы осуществления соединений при сборке изделий
В зависимости от вида производства применяют пять основных методов сборки: 1) при полной взаимозаменяемости деталей сборочных единиц; 2) с сортировкой деталей по группам (метод группового подбора); 3) с подбором деталей (неполная взаимозаменяемость); 4) с применением компенсаторов; 5) с индивидуальной пригонкой деталей по месту. Метод полной взаимозаменяемостипредусматривает сборку машин без какой-либо дополнительной обработки деталей с установкой и заменой любой детали без пригонки. Этот метод экономически целесообразен в массовом и крупносерийном производстве. При этом методе ускоряется сборка машин, снижается трудоемкость.Метод полной взаимозаменяемости предусма¬тривает сборку машин без какой-либо дополнительной обработки дета¬лей с установкой и заменой любой детали без пригонки. Этот метод экономически целесообразен в массовом и крупносерийном пр-ве, где кап. затраты на оснащение производства окупаются большим количеством изготовляемых машин. При этом методе бла¬годаря отсутствию операций подбора или пригонки деталей ускоря¬ется сборка машин, снижается трудоемкость и увеличивается выпуск продукции. Помимо этого, использование комплектов запасных деталей и узлов, изготовленных на основе полной взаимозаменяемо¬сти, обеспечивает быструю замену в эксплуатацион¬ных условиях изношенных или поврежденных деталей, что повышает эффектив¬ность эксплуатации машин. Метод сборки с применением сортировки деталей (метод группового подбора). Для осуществления высокой степени однородности посадок (без дополнительной пригонки деталей) и предотвращения увеличения затрат на производство при назначе¬нии излишне жестких допусков сборку ведут путем подбора (предва¬рительной сортировкой деталей). Этот метод, сборки применяют там, где по условиям работы деталей требуется зазор или натяг в более узких пределах, чем получаемый из основных размеров деталей с учетом допусков на их изготовление. В таком случае требуемый конструкцией зазор или натяг получают не за счет изготовления деталей с минимальными допусками, а путем соответствующего подбора охватывающих и охватываемых деталей, т. е. к отверстию с диаметром, близким к верхнему пределу, подби¬рают более полный вал и, наоборот, к отверстию с диаметром, близким к нижнему пределу, подбирают менее полный вал. Подбор деталей значительно упрощается, если детали обоих наименований по размерам (в пределах допусков на их изготовление) разбивают на несколько групп. Метод предварительной сортировки деталей на группы предусматривает разбивку полей допусков сопря¬гаемых деталей на несколько равных частей и подбора их таким обра¬зом, чтобы полномерные охватываемые детали сопрягались с полно¬мерными охватывающими деталями.Метод сборки с применением подбора дета¬лей (неполная взаимозаменяемость).Этот метод основан на учете ве¬роятностей отклонений размеров, составляющих размерную цепь, при-чем возможно получение некоторого количества сборочных единиц, выходящих за установленные пределы точности. Сборка с примене¬нием подбора деталей благодаря расширению допусков на все звенья размерной цепи позволяет экономичнее изготовлять детали. Метод сборки с применением компенсато¬ров. При большом числе звеньев размерной цепи и малом допуске замыкающего звена (зазора или натяга) необходимая для полной вза¬имозаменяемости точность изготовления деталей может в значитель¬ной степени усложнить производство и далеко выйти за пределы эко¬номически целесообразной точности. В таких случаях приходится либо отказаться от полной взаимозаменяемости, допуская пригонку деталей по месту, либо вводить в конструкцию механизма тот или дру-гой вид компенсатора, позволяющего регулировать в определенных пределах один из размеров. Такую регулировку называют компенса¬цией, а деталь, подбираемую в размерной цепи или специально вво¬димую в цепь для уменьшения допуска замыкающего звана, — ком¬пенсатором. Характерная особенность всех компенсаторов состоит в том, что сборка с их применением позволяет выдерживать установленные пре¬делы точности в размерной цепи путем изменения величины одного из ранее намеченных звеньев. Обработка же всех остальных звеньев цепи осуществляется по допускам, наиболее приемлемым для данных производственных условий. Величину компенсирующего звена можно регулировать двумя способами: введением в размерную цепь специальной детали—про¬кладки, шайбы, промежуточного кольца и т. п. (неподвижные компен¬саторы) и изменением положения одной из деталей, например клина, втулки, эластичной или пружинной муфты, эксцентрика и т. п. (под-вижные компенсаторы). Метод сборки с индивидуальной пригонкой деталей по месту.Сборка с пригонкой деталей по месту за¬ключается в том, что установленный предел точности замыкающего звена в размерной цепи достигается изменением величины одного из заранее намеченных звеньев путем снятия дополнительного слоя материала. По существу, сборка с доделкой деталей по месту является методом неполной взаимозаменяемости с пригонкой деталей в тех слу¬чаях, когда размер замыкающего звена лежит за пределами допу¬скаемых отклонений. Чтобы производить пригонку за счет выбранного компенсирую¬щего звена, необходимо: располагать поле допуска подлежащей при¬гонке детали относительно номинала с таким расчетом, чтобы обеспе¬чить на компенсирующем звене слой материала (припуск на пригонку), достаточный для компенсации величины превышения допускаемой погрешности замыкающего звена. Существенными недостатками метода сборки с пригонкой по месту являются: потребность в рабочих высокой квалификации; повышенная трудоемкость, иногда достигающая 40…50% общей трудоемкости сборки машины.28. Расчет количества основного технологического оборудования и рабочих мест для поточного производства
Расчет количества технологического оборудования для поточного производства производится по точной программе и предусматривает разработку подробного технологического процесса обработки или сборки с техническим нормированием выполнения к каждой операции на все изготовляемые изделия, входящие в программу выпуска. Расчет числа станков, необходимых для каждой операции, выполняют на основании штучно-калькуляционного времени и объема выпуска каждого наименования изделия, проходящего эту операцию, по формуле где n — число наименований изделий, проходящих данную операцию; tшт.к.i и Ni — соответственно штучно-калькуляционное время (мин) изготовления i-го наименования изделия на данной операции и ее годовой объём (шт.) выпуска; Фэ — эффективный годовой фонд времени работы основного оборудования, ч. Штучно-калькуляционное время где tоп.i — оперативное время изготовления изделия на данной операции, мин; tт.i — время, затрачиваемое на техническое обслуживание основного оборудования, отнесенное к одному изготовляемому изделию (время на замену, настройку и поднастройку инструмента, устранение неисправностей и т. п.), мин; tорг.i — время, затрачиваемое на организационное обслуживание основного оборудования (на подготовку технологического оборудования к работе, простои, связанные с несвоевременным получением полуфабриката, сбои с доставкой инструмента и т. п.), мин; tп.i — время регламентированных перерывов на отдых и естественные надобности рабочего, мин; Tп.з.i — среднее подго¬товительно-заключительное время, затрачиваемое на переналадку при переходе на операцию изготовления i-го изделия, мин; ni — партия запуска данных изделий, шт. При отсутствии данных по составляющим штучно-калькуля¬ционного времени можно пользоваться формулой где α — процент потерь времени (внецикловых) от оперативного времени — α = 6 … 18 % в зависимости от сложности наладки. При непрерывно-поточном производстве последняя составляю¬щая штучно-калькуляционного времени не учитывается, так как в данном случае отсутствует переналадка оборудования на другие наименования изделий. Вычисленное значение Ср округляют до ближайшего большего целого числа, получая при этом количество технологического оборудования Спр, принятое для выполнения данной операции. Коэффициент загрузки технологического оборудования kз на данной операции kз = Ср/Спр,, где Ср, Спр — оборудование соответственно расчетное и принятое. Следует учесть, что всегда коэффициент загрузки kз < 1. В случае незначительного превышения (на 5—10%) расчетного количества технологического оборудования над ближайшим целым числом необходимо пересмотреть содержание структуры выполне¬ния операции, параметры режимов ее выполнения и состава тех-нологического оснащения, что в итоге приведет к общему повыше¬нию коэффициента загрузки оборудования. Желательно, чтобы при проектировании поточного производства kз > 0,65. При расчете числа станций на сборочном конвейере необходимо учесть, что помимо рабочих станций на конвейере размещают 5—10% резервных для случая изменения конструкции собирае¬мого изделия.29. Пути повышения точности механической обработки
К основным факторам, оказывающим влияние на точность механической обработки заготовок, относятся: — неточность и износ оборудования (станка); — погрешность установки заготовки на станке; — упругие деформации технологической системы; — температурные деформации технологической системы; — остаточные внутренние напряжения; — неточность изготовления, установки и износ инструмента. Взаимосвязь указанных факторов и различная степень их влияния при различных методах обработки определяют точность механической обработки заготовок. Различные станки обеспечивают различную точность механической обработки. Неточность станка копирует обрабатываемая заготовка. Повышение точности станков можно, осуществить за счёт следующих мероприятий: — повышение точности шпиндельных узлов, их жёсткости (уменьшения расстояния между опорами), применение более точных подшипников качения и повышения точности посадочных мест, применения гидростатических подшипников; — повышения точности (равномерности) перемещений кареток и суппортов по направляющим, уменьшения зазоров в подвижных соединениях, применения антифрикционных материалов, направляющих качения с предварительным натягом и гидростатических направляющих; — повышения статической и динамической жёсткости корпусных деталей; — снижения влияния температурных деформаций узлов и деталей станка и обрабатываемой заготовки; — введения систем цифровой индикации, обеспечивающих точность отчёта перемещений режущего инструмента; — применение резцедержателей и инструментов, настраиваемых вне станка.30. Методы производства заготовок конических зубчатых колес и особенности их механической обработки
Бывают: 1) с прямым зубом: относительно не высокая нагрузка и не высокие скорости; 2)с криволинейным зубом(криволинейный зуб это круговой зуб. Дуга окружности з/в проходит через центр з/в): передача крутящего момента под углом; 3) гипоидная окружность смещена относительно центра: увеличенная дуга контакта, чтобы уменьшить удельное давление. Боковая поверхность зуба имеет эвольвентную форму. З/к с прямым зубом: Единственный метод обр-ки является зубострогание. В этом случае имеется центральная люлька, на которой располагаются резцы. Центр направляющих совпадает с центром люльки. Резец снимает тонкую стружку. Резцы имитируют коническое з/к, двигаясь возвратно-поступательно, по которым катится нарезаемое з/к. Заготовка поворачивается вокруг своей оси. Резцы имеют возвратно-поступательное движение и осуществляется обр-ка какой-то части з/к. При одном возвратно-поступательном перемещении снимается полоска не более 0.1мм. для того чтобы осуществить формирование зуба делается соответствующее вращение люльки. При этом з/к также катится и это обеспечивает постепенное строгание и формирование эвольвенты. Степень точности относительно не высокая 8-9квалитет; Rа=2,5мкм. Для повышения точности обр-ка ведется на зубошлифовальных станках таким же точно методом: Rа=0,16…0,32; 7-6квалитет; Vшлиф.=30..50м/с; съем 2 мм по методу обката. Ширина впадины по высоте переменна.
О сайте
Ссылка на первоисточник:
http://ens.mil.ru/education/news.htm
Поделитесь в соцсетях:
Оставить комментарий
Inna Petrova 18 минут назад
Нужно пройти преддипломную практику у нескольких предметов написать введение и отчет по практике так де сдать 4 экзамена после практики
Иван, помощь с обучением 25 минут назад
Inna Petrova, здравствуйте! Мы можем Вам помочь. Прошу Вас прислать всю необходимую информацию на почту и написать что необходимо выполнить. Я посмотрю описание к заданиям и напишу Вам стоимость и срок выполнения. Информацию нужно прислать на почту info@the-distance.ru
Коля 2 часа назад
Здравствуйте, сколько будет стоить данная работа и как заказать?
Иван, помощь с обучением 2 часа назад
Николай, здравствуйте! Мы можем Вам помочь. Прошу Вас прислать всю необходимую информацию на почту и написать что необходимо выполнить. Я посмотрю описание к заданиям и напишу Вам стоимость и срок выполнения. Информацию нужно прислать на почту info@the-distance.ru
Инкогнито 5 часов назад
Сделать презентацию и защитную речь к дипломной работе по теме: Источники права социального обеспечения. Сам диплом готов, пришлю его Вам по запросу!
Иван, помощь с обучением 6 часов назад
Здравствуйте! Мы можем Вам помочь. Прошу Вас прислать всю необходимую информацию на почту и написать что необходимо выполнить. Я посмотрю описание к заданиям и напишу Вам стоимость и срок выполнения. Информацию нужно прислать на почту info@the-distance.ru
Василий 12 часов назад
Здравствуйте. ищу экзаменационные билеты с ответами для прохождения вступительного теста по теме Общая социальная психология на магистратуру в Московский институт психоанализа.
Иван, помощь с обучением 12 часов назад
Василий, здравствуйте! Мы можем Вам помочь. Прошу Вас прислать всю необходимую информацию на почту и написать что необходимо выполнить. Я посмотрю описание к заданиям и напишу Вам стоимость и срок выполнения. Информацию нужно прислать на почту info@the-distance.ru
Анна Михайловна 1 день назад
Нужно закрыть предмет «Микроэкономика» за сколько времени и за какую цену сделаете?
Иван, помощь с обучением 1 день назад
Анна Михайловна, здравствуйте! Мы можем Вам помочь. Прошу Вас прислать всю необходимую информацию на почту и написать что необходимо выполнить. Я посмотрю описание к заданиям и напишу Вам стоимость и срок выполнения. Информацию нужно прислать на почту info@the-distance.ru
Сергей 1 день назад
Здравствуйте. Нужен отчёт о прохождении практики, специальность Государственное и муниципальное управление. Планирую пройти практику в школе там, где работаю.
Иван, помощь с обучением 1 день назад
Сергей, здравствуйте! Мы можем Вам помочь. Прошу Вас прислать всю необходимую информацию на почту и написать что необходимо выполнить. Я посмотрю описание к заданиям и напишу Вам стоимость и срок выполнения. Информацию нужно прислать на почту info@the-distance.ru
Инна 1 день назад
Добрый день! Учусь на 2 курсе по специальности земельно-имущественные отношения. Нужен отчет по учебной практике. Подскажите, пожалуйста, стоимость и сроки выполнения?
Иван, помощь с обучением 1 день назад
Инна, здравствуйте! Мы можем Вам помочь. Прошу Вас прислать всю необходимую информацию на почту и написать что необходимо выполнить. Я посмотрю описание к заданиям и напишу Вам стоимость и срок выполнения. Информацию нужно прислать на почту info@the-distance.ru
Студент 2 дня назад
Здравствуйте, у меня сегодня начинается сессия, нужно будет ответить на вопросы по русскому и математике за определенное время онлайн. Сможете помочь? И сколько это будет стоить? Колледж КЭСИ, первый курс.
Иван, помощь с обучением 2 дня назад
Здравствуйте! Мы можем Вам помочь. Прошу Вас прислать всю необходимую информацию на почту и написать что необходимо выполнить. Я посмотрю описание к заданиям и напишу Вам стоимость и срок выполнения. Информацию нужно прислать на почту info@the-distance.ru
Ольга 2 дня назад
Требуется сделать практические задания по математике 40.02.01 Право и организация социального обеспечения семестр 2
Иван, помощь с обучением 2 дня назад
Ольга, здравствуйте! Мы можем Вам помочь. Прошу Вас прислать всю необходимую информацию на почту и написать что необходимо выполнить. Я посмотрю описание к заданиям и напишу Вам стоимость и срок выполнения. Информацию нужно прислать на почту info@the-distance.ru
Вика 3 дня назад
сдача сессии по следующим предметам: Этика деловых отношений - Калашников В.Г. Управление соц. развитием организации- Пересада А. В. Документационное обеспечение управления - Рафикова В.М. Управление производительностью труда- Фаизова Э. Ф. Кадровый аудит- Рафикова В. М. Персональный брендинг - Фаизова Э. Ф. Эргономика труда- Калашников В. Г.
Иван, помощь с обучением 3 дня назад
Вика, здравствуйте! Мы можем Вам помочь. Прошу Вас прислать всю необходимую информацию на почту и написать что необходимо выполнить. Я посмотрю описание к заданиям и напишу Вам стоимость и срок выполнения. Информацию нужно прислать на почту info@the-distance.ru
Игорь Валерьевич 3 дня назад
здравствуйте. помогите пройти итоговый тест по теме Обновление содержания образования: изменения организации и осуществления образовательной деятельности в соответствии с ФГОС НОО
Иван, помощь с обучением 3 дня назад
Игорь Валерьевич, здравствуйте! Мы можем Вам помочь. Прошу Вас прислать всю необходимую информацию на почту и написать что необходимо выполнить. Я посмотрю описание к заданиям и напишу Вам стоимость и срок выполнения. Информацию нужно прислать на почту info@the-distance.ru
Вадим 4 дня назад
Пройти 7 тестов в личном кабинете. Сооружения и эксплуатация газонефтипровод и хранилищ
Иван, помощь с обучением 4 дня назад
Вадим, здравствуйте! Мы можем Вам помочь. Прошу Вас прислать всю необходимую информацию на почту и написать что необходимо выполнить. Я посмотрю описание к заданиям и напишу Вам стоимость и срок выполнения. Информацию нужно прислать на почту info@the-distance.ru
Кирилл 4 дня назад
Здравствуйте! Нашел у вас на сайте задачу, какая мне необходима, можно узнать стоимость?
Иван, помощь с обучением 4 дня назад
Кирилл, здравствуйте! Мы можем Вам помочь. Прошу Вас прислать всю необходимую информацию на почту и написать что необходимо выполнить. Я посмотрю описание к заданиям и напишу Вам стоимость и срок выполнения. Информацию нужно прислать на почту info@the-distance.ru
Oleg 4 дня назад
Требуется пройти задания первый семестр Специальность: 10.02.01 Организация и технология защиты информации. Химия сдана, история тоже. Сколько это будет стоить в комплексе и попредметно и сколько на это понадобится времени?
Иван, помощь с обучением 4 дня назад
Oleg, здравствуйте! Мы можем Вам помочь. Прошу Вас прислать всю необходимую информацию на почту и написать что необходимо выполнить. Я посмотрю описание к заданиям и напишу Вам стоимость и срок выполнения. Информацию нужно прислать на почту info@the-distance.ru
Валерия 5 дней назад
ЗДРАВСТВУЙТЕ. СКАЖИТЕ МОЖЕТЕ ЛИ ВЫ ПОМОЧЬ С ВЫПОЛНЕНИЕМ практики и ВКР по банку ВТБ. ответьте пожалуйста если можно побыстрее , а то просто уже вся на нервяке из-за этой учебы. и сколько это будет стоить?
Иван, помощь с обучением 5 дней назад
Валерия, здравствуйте! Мы можем Вам помочь. Прошу Вас прислать всю необходимую информацию на почту и написать что необходимо выполнить. Я посмотрю описание к заданиям и напишу Вам стоимость и срок выполнения. Информацию нужно прислать на почту info@the-distance.ru
Инкогнито 5 дней назад
Здравствуйте. Нужны ответы на вопросы для экзамена. Направление - Пожарная безопасность.
Иван, помощь с обучением 5 дней назад
Здравствуйте! Мы можем Вам помочь. Прошу Вас прислать всю необходимую информацию на почту и написать что необходимо выполнить. Я посмотрю описание к заданиям и напишу Вам стоимость и срок выполнения. Информацию нужно прислать на почту info@the-distance.ru
Иван неделю назад
Защита дипломной дистанционно, "Синергия", Направленность (профиль) Информационные системы и технологии, Бакалавр, тема: «Автоматизация приема и анализа заявок технической поддержки
Иван, помощь с обучением неделю назад
Иван, здравствуйте! Мы можем Вам помочь. Прошу Вас прислать всю необходимую информацию на почту и написать что необходимо выполнить. Я посмотрю описание к заданиям и напишу Вам стоимость и срок выполнения. Информацию нужно прислать на почту info@the-distance.ru
Дарья неделю назад
Необходимо написать дипломную работу на тему: «Разработка проекта внедрения CRM-системы. + презентацию (слайды) для предзащиты ВКР. Презентация должна быть в формате PDF или формате файлов PowerPoint! Институт ТГУ Росдистант. Предыдущий исполнитель написал ВКР, но работа не прошла по антиплагиату. Предыдущий исполнитель пропал и не отвечает. Есть его работа, которую нужно исправить, либо переписать с нуля.
Иван, помощь с обучением неделю назад
Дарья, здравствуйте! Мы можем Вам помочь. Прошу Вас прислать всю необходимую информацию на почту и написать что необходимо выполнить. Я посмотрю описание к заданиям и напишу Вам стоимость и срок выполнения. Информацию нужно прислать на почту info@the-distance.ru